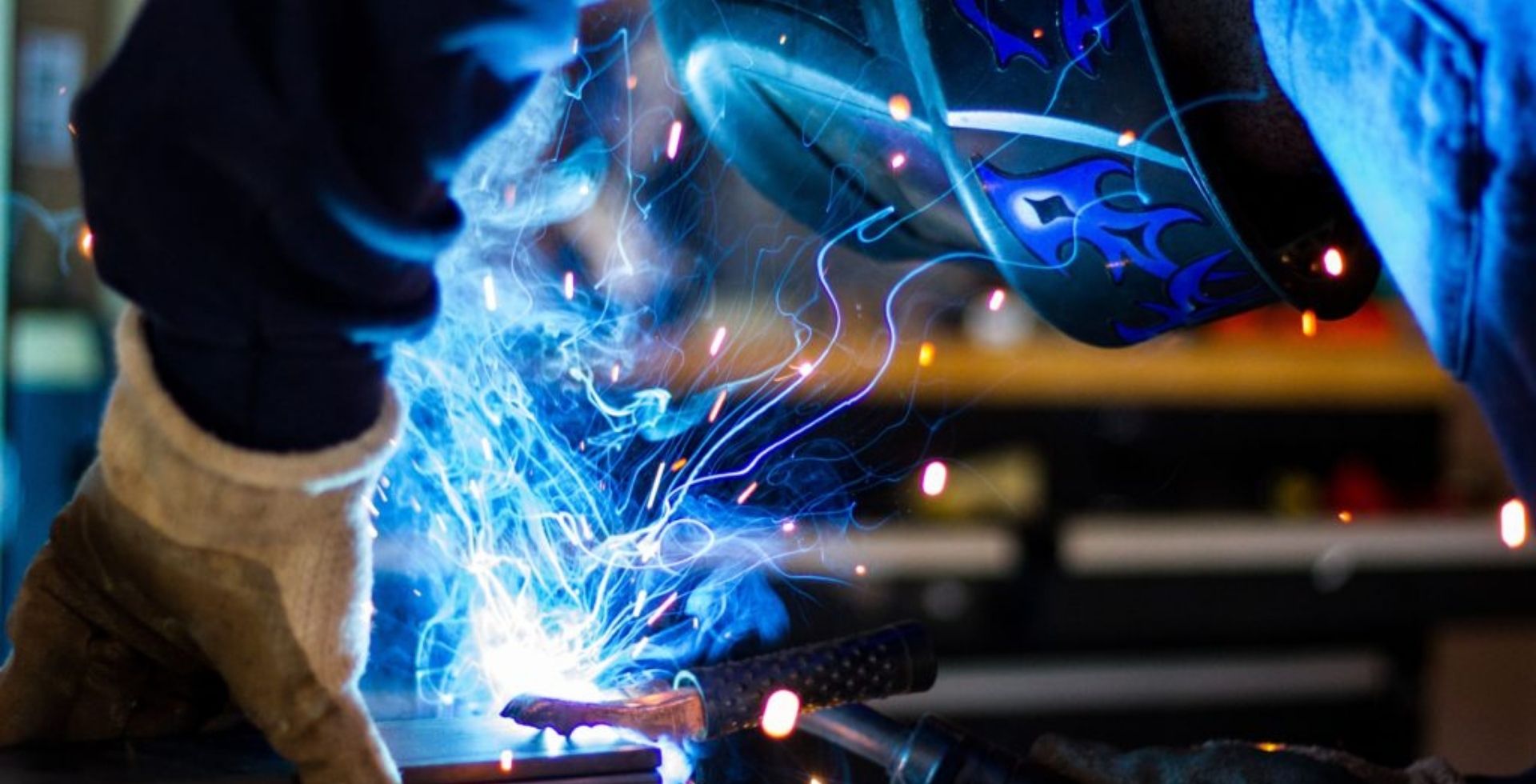
- 6 mai 2021
Véritable révolution pour les industriels, la maintenance prédictive apparait comme un puissant levier de performance dans la gestion des actifs. Découvrez la puissance de l’Intelligence Artificielle au service de l’industrie 4.0.
La maintenance au cœur des enjeux industriels
Maintenance corrective, préventive et prédictive : quelles différences ?
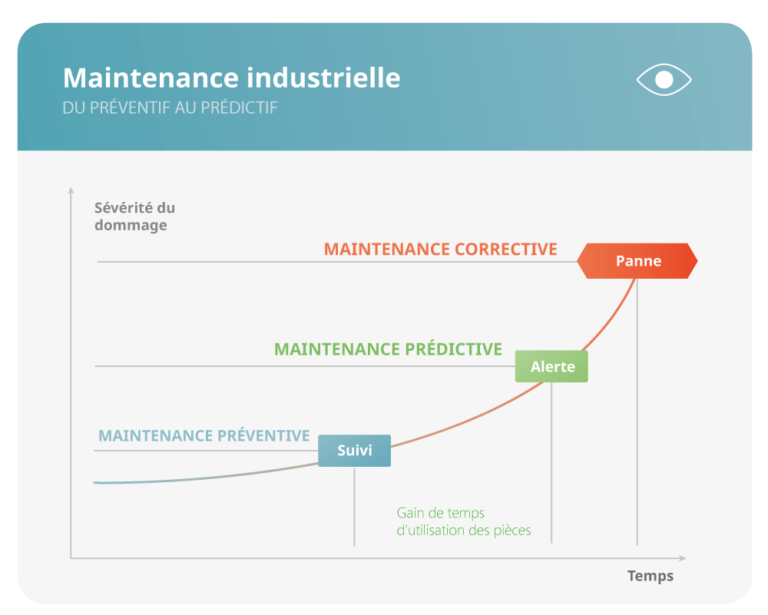
La maintenance corrective s’apparente au remplacement ou à la réparation des pièces lorsque celles-ci ont généré une panne. Cela impacte le bon fonctionnement de la chaine de production par des temps d’arrêt pour les opérations de maintenance non planifiées. En découle aussi le coût lié à la main d’œuvre associée.
Pour faire face à ces imprévus, grâce à la maintenance préventive, les industriels anticipent les pannes en organisant des opérations de maintenance régulières. Ce mode de fonctionnement classique est historiquement basé sur une démarche statistique. Ces opérations sont planifiées en fonction du MTBF (temps moyen entre les pannes). Cette démarche limite les imprévus car le remplacement de la pièce s’effectue avant sa fin de vie pour éviter l’instant fatidique de la panne.
Cependant, cette méthode n’est pas idéale car elle engendre des couts liés à la sous-utilisation des pièces. Il existe une alternative à ces deux méthodes grâce à la science des données : la maintenance prédictive.
Mais alors, qu’est-ce que la maintenance prédictive ?
Autrement appelée « maintenance prévisionnelle », celle-ci vient dépasser les limites de la maintenance corrective et de la maintenance préventive. Elle maximise le temps d’utilisation des pièces tout en anticipant les défaillances à venir grâce aux données collectées des équipements IoT.
De cette manière, la maintenance prédictive limite les pannes qui viendront impacter la chaine de production. Cette méthode agile permet de déclencher au moment opportun une opération de maintenance.
Pourquoi mettre en place la maintenance prédictive ?
L’intégration de la maintenance prédictive présente de nombreux avantages :
- Optimisation de la chaine de production en planifiant les opérations de maintenance des machines au bon moment
- Diminution des pannes
- Augmentation de la durée de vie des actifs d’exploitation
- Disponibilité de l’équipement ou du système optimisée
- Amélioration de l’approvisionnement des pièces de rechange afin de limiter l’excédent de stock
- Réduction des coûts afférents
- Accroissement de la satisfaction client grâce à un service de qualité dans les temps impartis
- Se rapprocher de l’excellence opérationnelle à travers la “zéro panne”
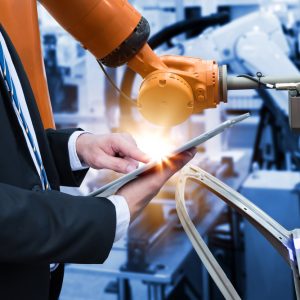
Face à cette multitude de bénéfices énoncés, vous êtes sans doute curieux sur la méthodologie de mise en place de la maintenance prédictive dans votre industrie et son retour sur investissement.
La démarche à suivre pour réussir son projet de maintenance prédictive
La maintenance prédictive : un investissement rentable ?
Nombreux sont les industriels qui ont déjà sauté le pas en termes d’équipements, notamment dans le secteur de l’aéronautique ou du transport ferroviaire. L’essor de l’industrie 4.0 liée aux mutations technologiques (notamment l’intégration d’équipements IoT et des données associées dans la stratégie globale) vient progressivement bouleverser tout le secteur industriel, des PME aux Grands Groupes.
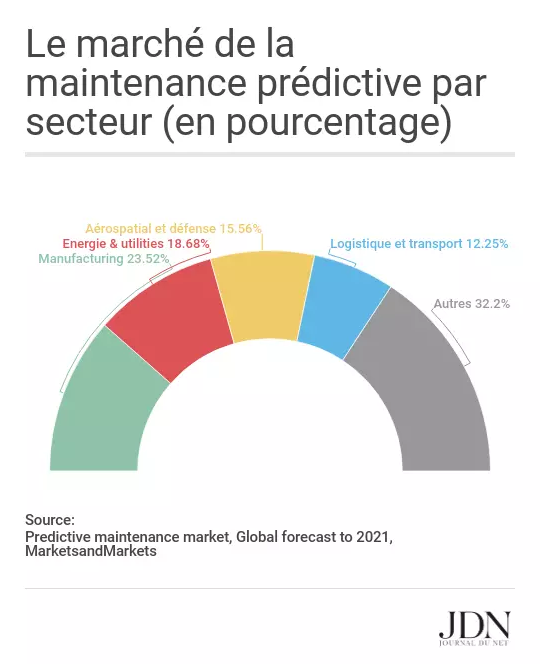
Pour rester à la pointe et ne pas manquer un virage crucial dans la vie de votre industrie notamment en ce qui concerne la maintenance, il est indispensable de prendre en considération l’enjeu de la maintenance prédictive.
En 2021, une étude OnePoll a été réalisée pour Reichelt Elektronik. Celle-ci démontre que 29% des entreprises sondées hésitent à adopter la maintenance prédictive en raison du coût.
La première question à se poser concerne directement votre usine et ses problématiques de maintenance.
Est-ce qu’il y a un véritable besoin ?
Si votre parc industriel contient peu de machines, vous pouvez peut-être vous contenter de la maintenance préventive. Cependant, comme nous l’avons vu auparavant, il faut être conscient des limites de cette méthode.
A contrario, si votre parc industriel est composé d’une centaine de machines et qu’il fabrique plusieurs milliers de références, la maintenance prédictive vous concerne directement. D’autant plus si les pannes de vos équipements ont des conséquences importantes sur la production, il peut être judicieux d’investir dans des équipements IoT qui permettront par la suite une analyse des données recueillies. Tel est le cas pour les industries spécialisées en automobile ou en métallurgie par exemple.
Concrètement, les couts d’un projet de maintenance prédictive peuvent être élevés et demandent un processus de changement fort en interne. Cependant, cet investissement est rapidement amorti car les retours sur investissements sont considérables.
Comment mettre en place la méthodologie de maintenance prédictive ?
Si vous souhaitez impulser une démarche de maintenance prédictive dans votre industrie, il est tout d’abord judicieux de se faire accompagner par des experts. C’est ce qu’a fait Cédric Picard, Directeur Général du Groupe Devillé Automotive sur sa problématique d’ordonnancement industriel afin d’éviter la surexploitation de ses machines. Vous pouvez retrouver son témoignage en cliquant juste ici.
Ensuite, il est important de réaliser un audit du fonctionnement de votre ligne de production ainsi que les solutions techniques de collecte de données dont vous disposez.
Ces données collectées en temps réel proviennent en général des équipements issus de l’environnement IoT . Ces données sont issues des instruments de mesure visant à réaliser des tests d’émission, l’imagerie thermique, la détection d’ultrasons, l’analyse de l’huile et de la vibration, etc. Elles sont ensuite centralisées dans le logiciel de pilotage de la production (GMAO) qui enregistre globalement l’activité des machines.
Une fois cette collecte de données réalisée, place à l’analyse ! C’est le moment d’identifier les causes des pannes pour mettre en place une maintenance prédictive efficace. C’est ici que l’Intelligence Artificielle entre en scène.
L’apport de l’intelligence artificielle dans l’industrie 4.0
Face à la surabondance des données collectées, il est parfois difficile de reconnaitre ceux qui sont en phase avec la problématique de maintenance. Le regard extérieur des datas scientists sur la base de données permet d’éviter tous les biais cognitifs des équipes internes à l’entreprise qui peuvent nuire à la pensée factuelle.
Dans ce processus d’analyse de données, il est aussi indispensable d’intégrer les experts métiers dans les échanges. Ces retours terrains sur le fonctionnement des machines notamment permettent à l’équipe d’experts en Intelligence Artificielle de déterminer un indice de criticité pour chaque composant à surveiller. Par exemple, pour l’un de nos clients, grâce à ses équipements en capteurs, nous avons identifié que les pannes provenaient de la qualité du sol (sol trop friable, présence de gaz de schiste etc).
Une fois que les données relatives à la panne ont été identifiées grâce à l’environnement de capteurs connectés , la collaboration entre votre équipe et celle des experts IA ne s’arrête pas là. Ils modélisent ensemble les schémas d’incidents et de défaillances propres à vos machines et plus globalement à votre usine. Ce travail collaboratif permet la mise en place d’un ou plusieurs algorithmes de Machine Learning dont la mission sera de prédire les pannes.
L’algorithme expérimente dans un premier temps les différents modèles grâce à un jeu de données déterminé. Plus celui-ci aura l’opportunité de s’entrainer, plus il sera performant dans la détection des pannes en temps réel. Il saura aussi s’adapter aux nouvelles situations qui n’auront pas été programmées au préalable, c’est ici toute la puissance de l’Intelligence Artificielle.
Lorsque cette phase de test sera terminée, les modèles de prédiction seront mis en production, connectés en temps réel à la GMAO existante.
Les facteurs clés de succès d’un projet de maintenance prédictive
Pour réussir votre projet de maintenance prédictive, rappelons que cet investissement pour l’avenir est un processus nécessitant un investissement important de la part des sociétés souhaitant en récolter les bénéfices. Il est important de considérer toutes les phases d’un projet d’une telle envergure.
Cependant, cette démarche agile d’industrie 4.0 tournée vers la zéro panne n’est pas illusoire. La mise en place de la maintenance prédictive dans les entreprises possédant de réelles contraintes de maintenance est rapidement rentabilisée.
Pour réussir, il est nécessaire d’investir dans des équipements IoT et d’impliquer les équipes techniques dans ce projet. Leur participation active à cette conduite du changement permettra d’avoir un retour terrain sur l’activité des machines au plus près de la réalité et de les accompagner dans l’adoption progressive de la maintenance prédictive.
En étant accompagné par des experts en Intelligence Artificielle, vous saurez mettre toutes les chances de votre côté pour que ce projet de maintenance prédictive soit un succès.