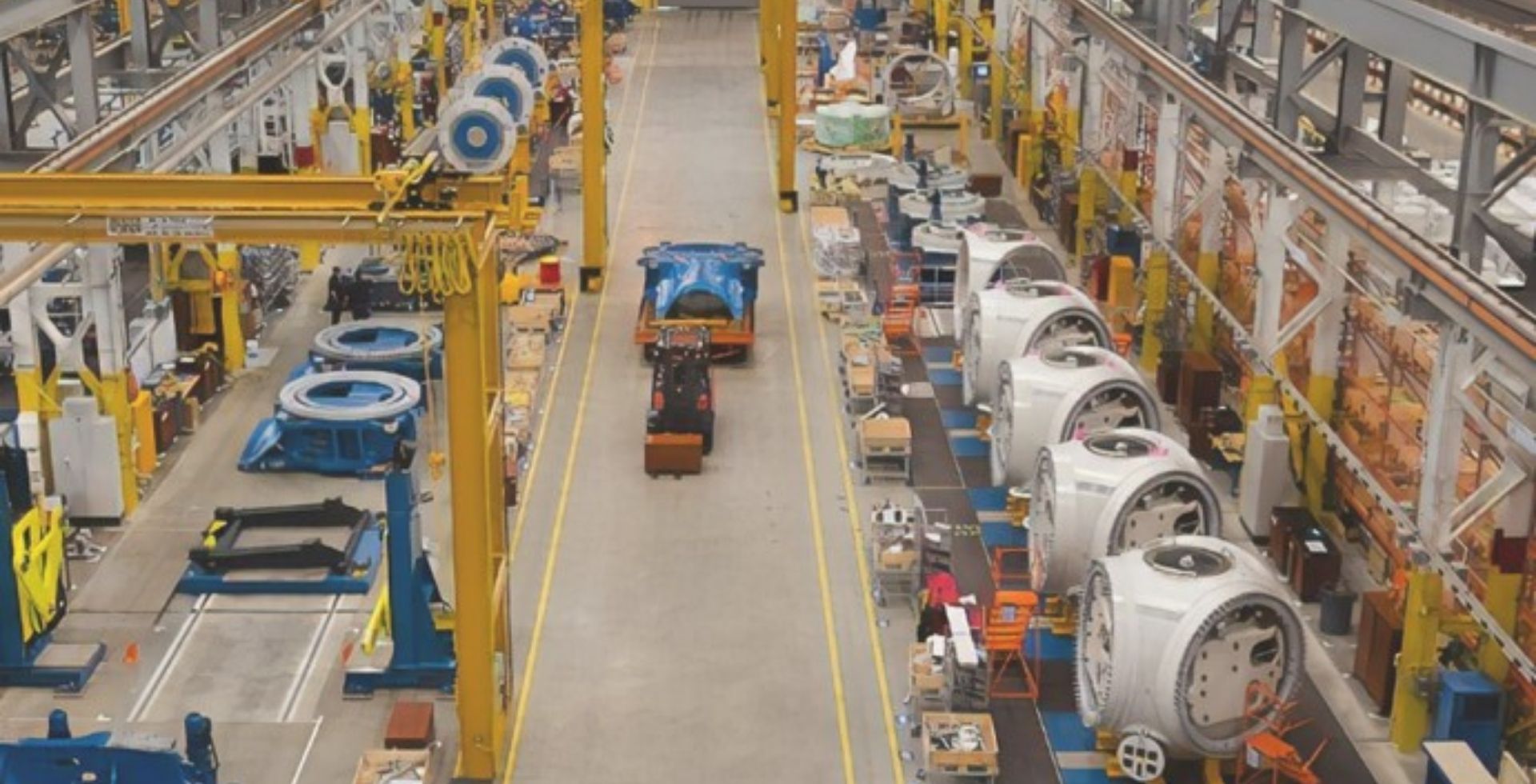
- 16 novembre 2020
Dans son usine composée d’une centaine de machines et fabriquant plusieurs milliers de références, la société Devillé a fait appel à Cross Data pour optimiser son processus de planification.
Découvrez la solution sur mesure que nous lui avons développée en 2 mois !
L’optimisation de la planification de production : véritable enjeu pour les industries
D’une manière générale, l’enjeu majeur de la gestion de production vise à prendre en compte à la fois la gestion des flux dans l’entreprise et les process opérationnels qui en découlent.
Pour fournir le produit demandé par les clients dans les délais prévus, l’entreprise doit faire face à des contraintes relatives à la bonne gestion du planning de production, la nature du produit et ses références, les performances des machines, etc.
En ce qui concerne notre client, son usine livre ses clients en temps et en heures mais le processus de planification n’est pas optimisé.

Dans la situation présente, les chefs d’ateliers sont fortement sollicités et donc confrontés à une part importante de planification dans leurs journées. Les conséquences sont multiples et touchent tous les services : potentiels retards internes, gestion trop récurrente en mode urgence et taux de rendement synthétique (TRS) optimisables.
Mais alors comment améliorer ces process de planification industrielle avec l’IA et la Data ?
Pour l’équipe de Cross Data, le constat était simple. Il fallait faciliter la vie des équipes en leur fournissant une solution rapide et surtout internalisable. Cette solution adaptée et économique permet aussi d’éviter l’achat de licences à un coût prohibitif.
L’efficacité industrielle : optimiser les process grâce à l’IA et la Data
Nos experts en Data & IA ont envisagé plusieurs solutions pour répondre aux besoins de notre client.
Dans un premier temps, nous avons imaginé utiliser les modules issus de l’ERP déjà existant. Cependant, nous nous sommes rapidement aperçus que cela ne répondait qu’en partie à la requête exprimée. Celui-ci n’avait pas de fonctions d’optimisation adaptées à son besoin.
D’autre part, après une phase de test, l’utilisation d’une solution existante du marché ne s’est pas révélée être pertinente. En effet, l’algorithme (relativement onéreux) était trop lourd et par conséquent trop lent. Or, notre client souhaitait avoir une solution rapidement opérationnelle et clés en main.
C’est pourquoi le client a opté pour le développement d’une solution sur mesure et adaptée aux méthodes et logiciels déjà existants.
Notre solution sur mesure internalisable avec un ROI facilement identifiable
Avant d’entamer la création d’une solution, nous avons pris le temps d’échanger avec notre client sur son fonctionnement. Ensemble, nous avons pu mettre en avant les process pertinents à maintenir ainsi que les points à améliorer.
Nous avons créé un algorithme de calcul du plan de charge prenant en comptant la capacité maximale des machines. Cet outil permet d’optimiser les ressources (humaines, matérielles et financières) ainsi que le temps de travail des salariés.
Sur le plan technique, notre équipe a fait le choix de modéliser le problème comme un PLNE (programme linéaire en nombres entiers), problème qui a pu être résolu par un solveur sous licence libre.
Le livrable fourni répond tant aux besoins opérationnels que techniques de notre client. Cette solution sur mesure lui permet d’obtenir un retour sur investissement significatif.
En effet, il peut visualiser sur son tableau de bord personnalisé, les gains réalisés par l’algorithme.
Résultat : une amélioration significative de la planification
Cette solution est une réussite pour plusieurs raisons.
Tout d’abord, nous pouvons observer une réduction importante de la charge des machines et équipes trop sollicitées en la lissant sur d’autres machines du parc.
Sans communiquer les résultats précis, les indicateurs clés principaux ont été améliorés de plus de 30 %. Cela engendre naturellement une réduction des coûts afférents (notamment en termes d’heures supplémentaires).

En outre, sur le plan temporel, le temps de calcul est très rapide : il faut moins d’un dixième de seconde à l’algorithme pour calculer la planification de la semaine.
D’autre part, grâce à l’interface, notre client a pu obtenir une vision globale de son activité en visualisant simplement le fonctionnement de ses machines toutes les semaines. L’étude de la charge planifiée lui a permis de réaliser que certaines machines étaient en surcharge permanente.
Cela a facilité l’équilibrage des productions entre différents moyens compatibles et de faciliter des changements d’organisation visant à augmenter l’efficacité industrielle. De plus, cette analyse aide notre client à réfléchir sur ses potentiels investissements futurs.
Vous l’aurez compris, en intégrant les algorithmes et la Data à son fonctionnement, notre client a pu gagner du temps et obtenir un véritable retour sur investissement.
Conclusion
Pour conclure, avec Cross Data, notre client a pu améliorer durablement ses process de planification industrielle avec une solution, rapide, simple et efficace. Déployée en 2 mois, elle aura permis à Devillé de mettre en œuvre des économies précises et une amélioration de la qualité de travail.
Cette phase relative au recalcul du plan de charge est une première étape dans le projet. Nous prendrons ensuite en compte la gestion des retards et enfin la planification. La phase de planification permettra à notre client d’ordonnancer les références sur les machines afin de respecter les contraintes qui leur sont affairées.
Et comme nous le disons souvent chez Cross Data, pas de projet sans retour sur investissement !
Vous voulez en savoir plus ?